Sterling provides a wide selection for all of your material handling needs including central drying systems.
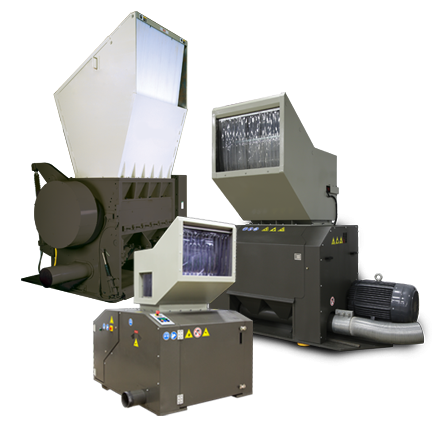
Sterling provides a wide range of size reduction equipment and systems utilized in injection molding, thermoforming, extrusion and recycling facilities. Products include beside-the-press, below-the-press, central and heavy-duty granulators along with single or multi-stage shredders. A variety of sizes and configurations are available, offering a wide range of material throughput. These machines produce exceptional regrind to maximize resin reclaim while keeping maintenance costs low, reducing downtime and enhancing operator safety. Sterling’s granulators are available for hand, robot or conveyor feed applications. The Sterling team of size reduction experts can create integrated regrind evacuation systems designed specifically for your operation.
Granulators
Beside the Press Granulators
Each machine integrates into any molding or extrusion operation for resin reclaim directly at the side of the press. Sterling beside-the-press granulators are equipped with or without screens to allow optional viewing of material being processed. The screens give the ability to gauge how full the cutting chamber is and verify consistent material flow without having to shut the machine down. Design your system with a variety of customizable options such as infeed and discharge configurations.
Download the complete product brochure
FX700 Series Beside-the-Press Granulators
Sterling’s Beside the Press FX700 Series allows easy access to the screen cradle and cutting chamber. The rotor is wide open, making cleaning and knife changes quick and easy. An improved discharge seal minimizes regrind leakage, while a larger discharge bin offers more uptime. Optional viewing windows on the hopper offer the opportunity to watch material being processed. This gives you the ability to gauge how full the cutting chamber is and verify consistent material flow without having to shut the machine down.
Superior Maintenance Access
- Industry leading access to cutting chamber and screen cradle
- Improved all discharge seals and increased manual bin volume
- Optional hopper viewing windows for instant visual of the cutting chamber
Application Flexibility
- Configure your system with a variety of customizable options such as infeeds, hopper styles, and evacuation systems
Enhanced Safety
- Optional category 3 redundant safety circuit with 2 sets of contacts, short circuit protection, meets ISO-12100 standards
- Hopper viewing windows (optional) and sound dampened enclosures
FX1000 Series Beside-the-Press Granulators
Sterling’s Beside the Press FX1000 Series allows easy access to the screen cradle and cutting chamber. The rotor is wide open, making cleaning and knife changes quick and easy. An improved discharge seal minimizes regrind leakage, while a larger discharge bin offers more uptime. Optional viewing windows on the hopper offer the opportunity to watch material being processed. This gives you the ability to gauge how full the cutting chamber is and verify consistent material flow without having to shut the machine down.
Superior Maintenance Access
- Industry leading access to cutting chamber and screen cradle
- Improved all discharge seals and increased manual bin volume
- Optional hopper viewing windows for instant visual of the cutting chamber
Application Flexibility
- Tangential and offset chamber geometry provides flexibility to size the chamber to your exact production needs
- Configure your system with a variety of customizable options such as infeeds, hopper styles, and evacuation systems
Enhanced Safety
- Category 3 redundant safety circuit, with 2 sets of contacts, short circuit protection, meeting ISO-12100 standards
- Zero speed monitoring
FX1600 Series Beside-the-Press Granulators
Sterling’s Beside the Press FX1600 Series allows easy access to the screen cradle and cutting chamber. The rotor is wide open, making cleaning and knife changes quick and easy. An improved discharge seal minimizes regrind leakage, while a larger discharge bin offers more uptime. Optional viewing windows on the hopper offer the opportunity to watch material being processed. This gives you the ability to gauge how full the cutting chamber is and verify consistent material flow without having to shut the machine down
Superior Maintenance Access
- Industry leading access to cutting chamber and screen cradle
- Improved all discharge seals and increased manual bin volume
- Hopper viewing windows for instant visual of the cutting chamber
Application Flexibility
- Tangential and offset chamber geometry provides flexibility to size the chamber to your exact production needs
- Configure your system with a variety of customizable options such as infeeds, hopper styles, and evacuation systems
Enhanced Safety
- Category 3 redundant safety circuit, with 2 sets of contacts, short circuit protection, meeting ISO-12100 standards
- Hopper viewing windows and sound dampened enclosures
S10 Series Beside-the-Press Granulators
Sterling’s S10 Series Screenless Granulator is known for its high quality regrind in sprue and runner reclaim applications. The S10 Series Granulator has a very low rpm speed roter helping to reduce waste by providing clean regrind to reuse in your process, and allows for energy savings. Stainless steel parts clean up fast and reduce maintenance costs. This compact footprint granulator will easily fit into your process flow.
Low Noise
- Sound proof steel hopper results in less noise pollution
- Low rotor RPM also contributes to less noise made within the chamber
Low Dust
- Rotating blade uses stainless steel, produces uniform grain size and minimizes powder formation
Energy Efficiency
- Newly designed cutter allows for energy efficient, consistent granulation while using less horsepower